28.11.2017
5 Reasons the Automotive Industry Needs Humidification
The automotive industry, specifically its manufacturing applications, comprises of a wide array of facilities and spaces carefully engineered for different purposes. From paint applications to sanding decks and engine testing areas, each facet of the automotive, industrial environment requires absolute humidity control to safeguard not only product quality but also the safety and wellness of employees to protect established productivity standards. Here are 5 key reasons why the automotive industry needs proper humidity control.
Reduced Electrostatic Discharge (ESD) Risk
Automotive industrial applications require the use of sensitive electronics and mechanical equipment to perform high-precision tasks. When static builds up in these environments through conductive surfaces, it can spell certain danger for individuals and the materials they are working on. Depending on the circumstances, electrostatic discharge (ESD) can cause major workplace damage, injuries, and even fatalities (such as when working with combustible/explosive materials). Maintaining relative humidity (RH) levels between 40% and 60% will greatly reduce the risk of electrostatic build-up, ensuring that materials, products, and applications remain unaffected, in turn safeguarding productivity and substantially reducing static transference-related safety risks to employees.
Safeguard Employee Health (Reduced Absenteeism)
In environments where a variety of processes are occurring such as sanding, paint spraying, and welding, airborne particles can pose a serious threat to employee health and safety when not combated with proper humidity control. Additionally, the same principle applies to airborne bacteria such as influenza. To protect employees from ingesting chemicals, dust, bacteria or other particles, maintaining consistent relative humidity control at 40% to 60% RH is crucial. This is because these levels minimize the amount of time particles and bacteria spend airborne, causing them to settle on surfaces far more quickly. This protects employee health, comfort, and wellness, therefore reducing absenteeism and ensuring efficient production rates.
Limit Attraction of Airborne Particles to Surfaces
Automotive manufacturing spaces have understandably strict quality control standards that must be followed to meet market and customer expectations. The introduction of dust or other airborne particles to surfaces such as vehicle bodywork can interfere with these standards and produce less-than-desirable results. Additionally, sensitive internal components such as electronics and vehicle engines require dust and particle-free installations to protect against the development of performance-related issues, which would reduce the lifespan of each respective part that is affected and could lead to various malfunctions. Maintaining 40% to 60% RH will ensure that the affect airborne materials have on sensitive surfaces and items is minimized to the fullest extent, making it far easier to maintain quality control according to established automotive manufacturer standards.
Protect Coating Quality and Adhesion
With paint applications and other forms of coating, specific humidity control is required to maintain adhesion as required consistently. This can impact vehicle aerodynamics, appearance, material wastage, and the potentiality of coated materials passing quality assurance with a seal of approval. Proper humidity control (72% RH) will prevent the evaporation of water-based paint so that it reaches the bodywork of a vehicle as intended by the manufacturer. Additionally, it greatly reduces the introduction of paint dust to paint spray booths, protecting materials, products, and employees. The quality of the final product is therefore higher, material wastage is kept at a minimum, and production speed remains unaffected.
Ensure Accurate Exhaust Emission Testing Results
When engine exhaust emission tests are carried out, the testing spaces themselves must receive absolute humidity control to guarantee the most accurate and reliable results. Temperature also plays a role in affecting what measurements are made and how consistent the collected data is with established exhaust emission standards. Maintaining proper humidity control as well as with evaporative cooling can provide absolute temperature and air moisture regulation, meeting required RH levels for comprehensive testing. This will protect against the wastage of time and resources, negating the need for excessive testing due to inaccurate, erratic or fluctuating results that just don’t seem to add up, which can be a direct result of a lack of humidity control.
Humidity in the automotive industry, particularly in manufacturing processes, benefits a wide variety of important factors that drive businesses forward. Employee health and absenteeism are safeguarded, as is final product quality and customer satisfaction. Additionally, efficiency and production rates are more easily maintained at consistently high levels, while workplace safety and material/product wastage are kept firmly under control. Condair’s humidifiers are available in a wide variety of load sizes and configurations, including evaporative cooling and gas-fired steam variants. For lower operating costs, greater efficiency, and the best results, proper humidity control through systems such as those by Condair can make all the difference. Contact us to learn more about how our energy efficient and clean humidification systems can benefit you today.
Helpful Links:
-
https://www.condair.com/why-humidify-importance-of-humidification/
-
https://www.condair.com/why-humidify-importance-of-humidification/Psych%20Charts
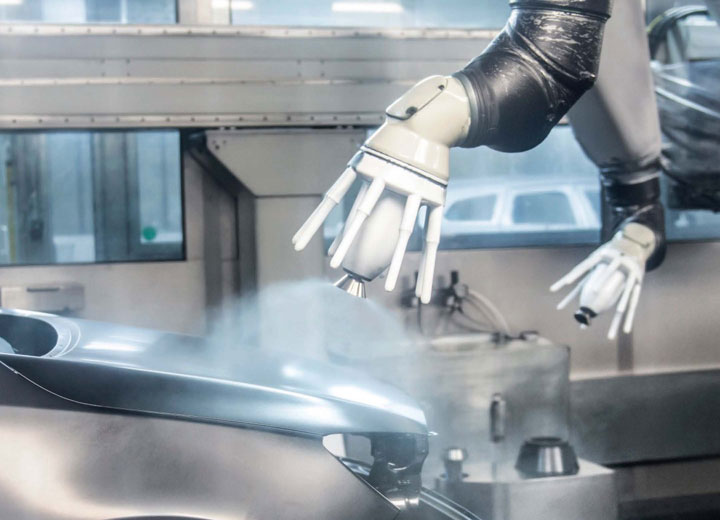
