21.08.2017
Ensure Wind Energy Manufacturing Consistency with Humidity Control
Wind energy production requires utmost efficiency and consistency in order to remain a viable and effective means of green energy production, and this extends right back to the manufacturing process. If sensitive components are exposed to fluctuating levels of humidity and a general lack of hydration control, they can encounter various performance detractors and inefficiencies. A precisely controlled humidity enables for wind energy manufacturing systems to perform at their peak, improving production output, elevating product quality and effectively boosting ROI. Here are some specific ways that humidity control can make a positive difference.
Improved Dust Suppression
When dry air infiltrates a composite manufacturing environment such as those for blades, it can cause surfaces to become charged with static electricity. Dust is also carried through the air with relative ease, as well as pollutants. In effect, this can produce a bevy of problems including dramatic static explosions and even dust fires. During the sanding process in particular, this can spell certain danger in uncontrolled environments.
A production facility with a sufficient and controlled level of humidity of 40-60%RH is able to suppress dust development, binding airborne particles and causing them to immediately fall to the ground where they can simply be swept away during normal cleaning processes.
Additionally, airborne fire dusts, odors and combustible materials are relegated away from contact with employees through properly controlled humidification, making for a healthier and infinitely safer workplace.
Employees with allergies or breathing difficulties will find it easier to focus and not succumb to illnesses brought on by overly moist or dry environments, which will bolster the effectiveness of any facility’s production and quality control even further.
Consistent Quality Paint and Coating Application
Additionally, specialized paints and finishes are negatively affected by static charge build-up, stemming from inadequate humidification. This is most prevalent in the form of inconsistently adhered coatings, which creating surface bumps and detracting from performance and efficiency.
For environments dedicated to such processes, it is important to maintain 70%RH to better maintain quality consistency and adherence, particularly during painting and coating application processes. Otherwise irregularities can pose a threat to energy efficiency and generate drag. Also, consider the fact that electrostatic painting and powder coating booths are now being widely implemented in manufacturing facilities across North America, which rely heavily on the maintenance of consistent humidity levels. If the RH is out of control or imbalanced, then higher flow rates are required for the same finish, eating into budgets and manufacturing productivity.
Static Elimination in Electronics Assembly
Electrostatic discharge (ESD) stemming from low humidity doesn’t just affect paint coatings and dust suppression, but also the effectiveness and safeguarding of sensitive electronic components. ESD occurs when the sudden flow of electricity between two electrically charged objects merges or breaks the dielectric down between them, triggering a visible spark. This can cause irreparable damage to electronics and sensitive components of a conductive nature.
Maintaining a consistent humidity level between 40-50%RH dramatically lowers surface resistance on products and equipment, as well as on floors, carpets, mats and areas directly met with human traffic. Not only will this protect electrical components, but it will also make electronics assembly facilities safer to work in by negating the risk of ESD. In turn, this helps to protect employees from harm and products from damage or defects, allowing for a consistent and uninterrupted production process free of risk.
Improved Energy Efficiency and Cost Savings
Evaporative cooling involves a highly efficient humidification process, and it is highly recommended to maintain wind energy manufacturing consistency. It introduces clean liquid water directly into the atmosphere while bypassing the standard requirement for thermal energy to be added. Without a need for heat in order to operate, they help to drastically reduce energy costs without reliance on expensive heating systems in order to function.
Regardless of whether you opt for a direct or indirect evaporative cooling system, you can be guaranteed of a cool and controlled interior temperature that also boasts stable humidity levels. This will enable for manufacturers to better maintain and improve product quality, decrease waste from damaged components, reduce heating bills, consume less energy and boost ROI of facility production and operations through effective and reliable humidity control that doesn’t feed off of thermal influence.
Any manufacturer can benefit from stable and precisely controlled humidity, including through direct and indirect evaporative cooling systems such as those engineered by Condair, but those working on wind energy components require the ultimate solution. LM Wind Power, Siemens, Vestas and GE have all implemented our reliable and highly efficient systems to improve their productivity and boost ROI, and others can benefit in the same manner by investing in humidification systems that better control quality, safety and production output. Contact us today to ensure you have the most efficient and beneficial humidification solution for your wind energy manufacturing facility.
Helpful Links:
Why Humidify…For Wind Energy
Why Humidify…For Wind Energy (PDF)
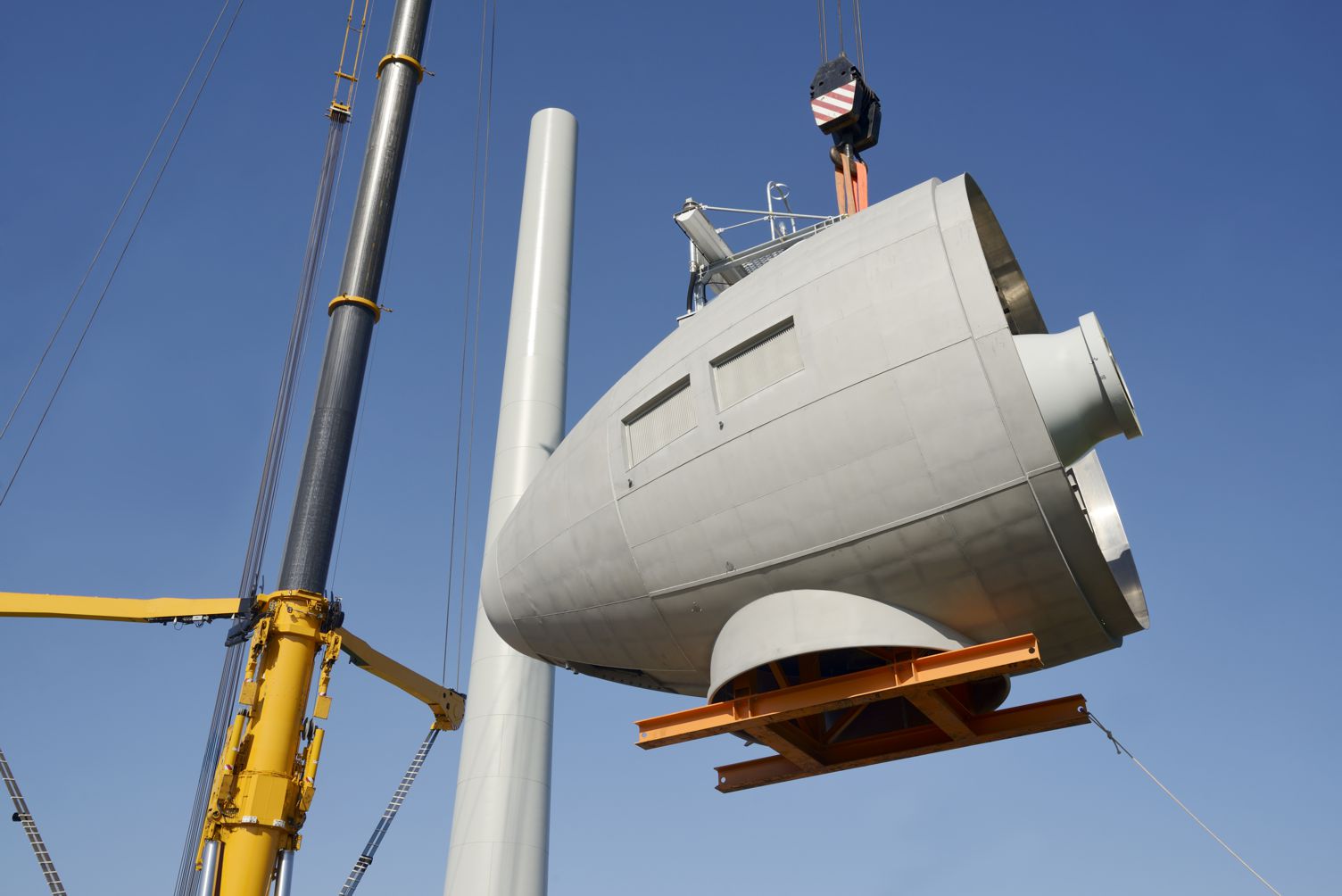
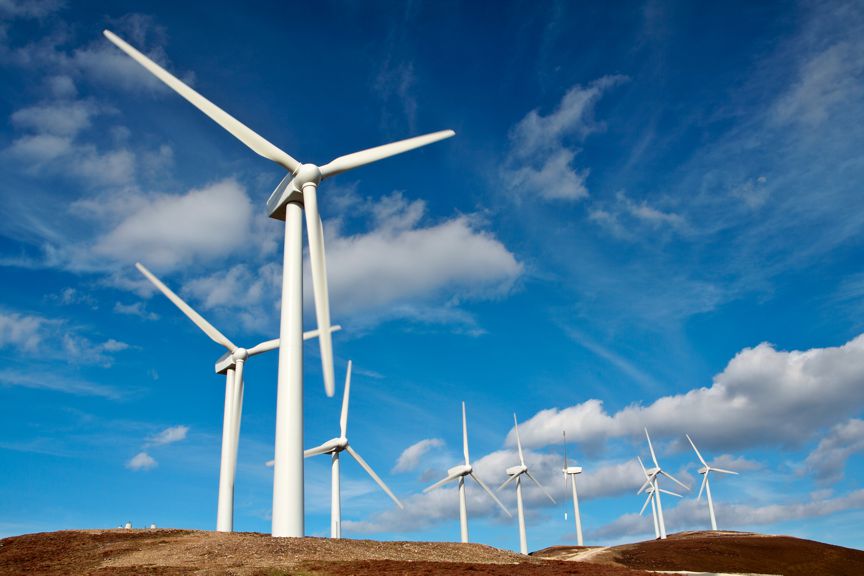